Research
Overview
The overarching objective is to develop fast methods for holistic virtual optimization of structures. In terms of a virtual process chain, further developments are required in three areas:
-
Fast data-driven approximation of manufacturing effects
-
Accelerated structural optimization methods
-
Integration of life cycle assessment in design process
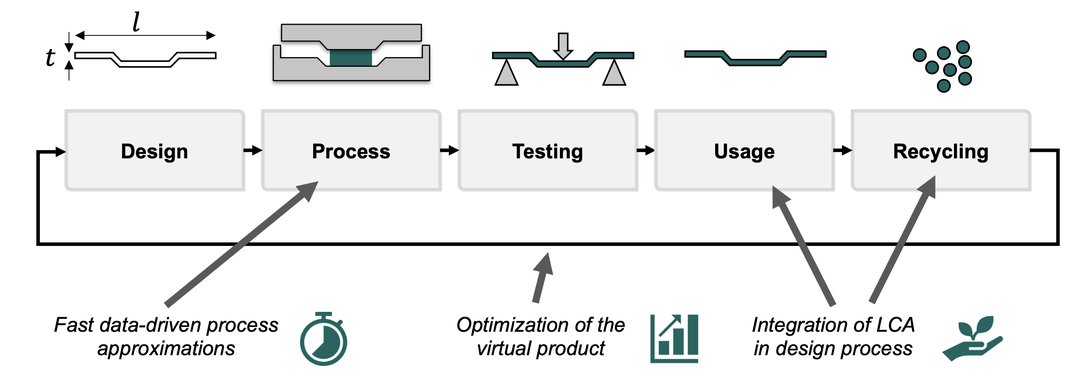
Fast data-driven approximation of manufacturing effects
In the case of structures made of complex structured materials, such as fiber composites, the manufacturing process has a major influence on the local properties of the component. Although these effects can be predicted virtually using process simulations, such simulations are too computationally intensive for algorithmic optimization of the component in many iterations. We are therefore developing data-driven methods for the rapid approximation of such effects.
Examples:
- Fast approximation of mold filling processes of discontinuously reinforced fiber-reinforced composites with machine learning
- Bayesian optimization of printing parameters in ceramic 3D printing
Accelerated structural optimization methods
Conventional structural optimization methods are usually iterative procedures with high computing times. We use machine learning methods and automatic differentiation frameworks to speed up optimization.
Examples:
- Patch Optimization with differentiable FEM
- Physics Informed Neural Networks for shape optimization
- Convolutional Neural Networks for topoloy optimization
Fiber Patch Placement
Integration of life cycle assessment in design process
The lightest component requires less material and reduces emissions during use, but is it always the most environmentally friendly? Sometimes it can make sense to design a component in such a way that it is slightly heavier in the short term, but can be better reused in a second life. We are researching how we can optimize products holistically (including recycling/reuse/remanufacturing).