CMC Processing
Contact person
- Phone: +49 821 598-69220
- Email: dietmar.koch@uni-auni-a.de ()
- Room 3013 (Building W)
Research topics
The "Liquid Silicon Infiltration (LSI)" method is often used to produce non-oxide fiber-reinforced ceramics (Ceramic Matrix Composites - CMC) with a silicon carbide (SiC) matrix. In this process, a polymer matrix is thermally cross-linked and pyrolyzed. The resulting carbon matrix is then infiltrated with liquid silicon, which reacts with the carbon to form SiC. The result is an inhomogeneous matrix with low residual porosity, which can contain SiC, carbon and free silicon. Optimizing the phase composition of the matrix can improve the failure behaviour, the elastic characteristics and the high-temperature resistance under aggressive atmospheres. Another important aspect of LSI processing is the protection of the reinforcing fibers, e.g. SiC or carbon fibers, against the reaction with the liquid silicon in order to avoid degradation of their mechanical properties.
The research activities of the "CMC Processing" working group are aimed at improving process control in the LSI process. The aim is to reduce the residual carbon content of the matrix in SiC/SiC materials in order to improve the stability of the material at high temperatures in an oxygen-containing atmosphere. An adaptation of the matrix polymer is promising here in order to enable uniform infiltration of the carbon with silicon. In addition, the SiC reinforcing fibers should be protected against attack by the silicon, e.g. through more gentle processing at reduced temperatures. In C/C-SiC materials, optimization of the crack structure of the carbon matrix is of interest to protect the carbon fibres. Another important field of research is the use of alternative C-rich precursors and recycled raw materials in order to make the LSI manufacturing process more sustainable.
Online monitoring of the material and process properties during the carbonization and silicification process is carried out in a high-temperature furnace equipped with sensors in order to gain a comprehensive understanding of the process.
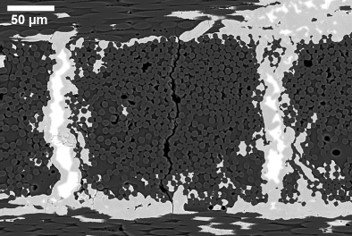
The areas of application for CMC materials include high temperatures of up to 1600°C and aggressive atmospheres. For this reason, the fiber-reinforced ceramics produced are also subjected to materials science tests under corresponding conditions. Of particular interest here is mechanical testing at high temperatures, which is currently being set up by the working group.