RG Processes
Group leader
- Phone: 0821 / 598 - 69168
- Email: joel.schukraft@mrm.uni-augsburgmrm.uni-augsburg.de ()
- Room 2011 (Building W)
- Phone: +49 821 598 - 69177
- Email: kerstin.dittmann@mrm.uni-augsburgmrm.uni-augsburg.de ()
- Room 2016 (Building W)
Research
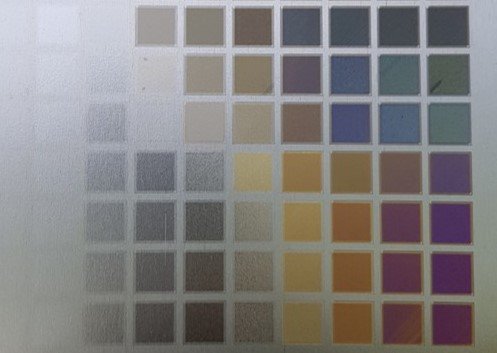
Material properties are essentially process-induced and the scientific penetration of the influence of process parameters on material properties is an important aspect for the elucidation of process-structure-property relationships. For this superordinate research and development focus at the Institute part “STAS”, the "Processes" research group produces hybrid composites and material composites using innovative processes and monitors them online using adapted sensor technology. The comparatively higher material costs of hybrid materials continue to require new, efficient manufacturing processes that make the best possible use of the material potential.
For a further development and combination of different classes of materials, the research group is working on the development of new production routes for the manufacture of hybrid materials, i.e. polymer/metal/ceramic-based composites and material composites. Special attention is paid to the implementation of processes that allow in-situ hybridization - thus eliminating the need for subsequent joining operations. To realize such routes, special attention must be paid to the adapted interface design (realized e.g. by laser structuring): On the one hand, this allows an optimal adhesion between the hybrid partners and, on the other hand, in terms of sustainability, the removal of the hybrid at the end of its life cycle - for example, via "switchable" interfaces - can be achieved.
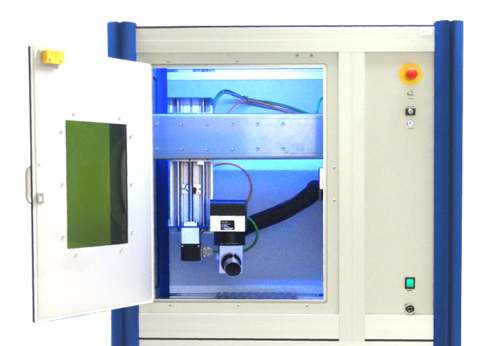
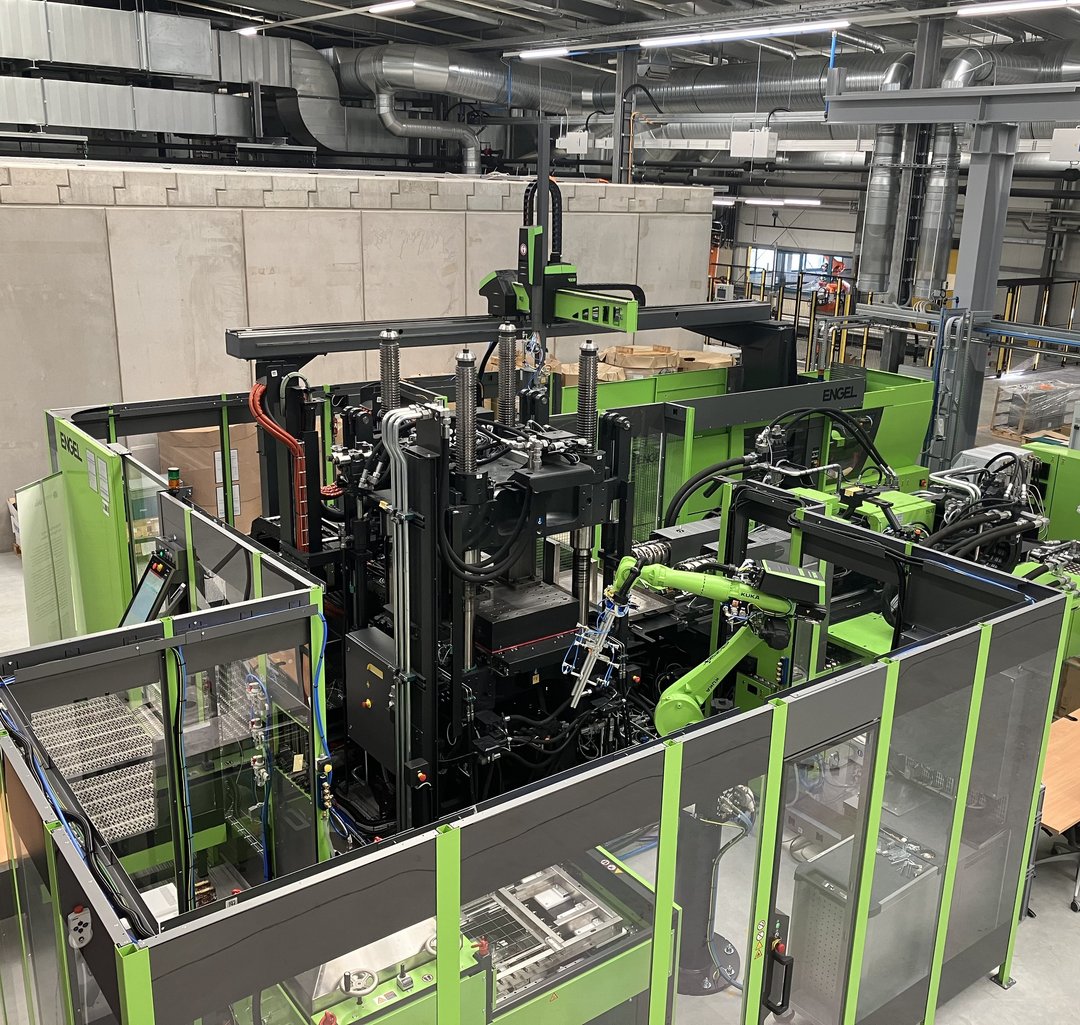
The processes themselves, on the other hand, should be capable for series production and recycling, which is why thermoset and thermoplastic-based injection molding in particular form the basis for the research activities. At the same time, a combination with generative manufacturing processes in the field of preforming or with metallic inserts is conceivable here. This leads to a further optimization of material utilization and can be implemented in a wide range of processes on the hybrid injection molding cell with plastic and metal processing side, an infrared oven, complete automation by two robot arms, as well as multi-component injection molding and foam injection molding on the plastic side. Last but not least, these processes also allow secondary raw materials to be recycled into the end product and thus partially recycle the materials, which the working group tackles by means of shredding and extrusion in batch size. In this context, the working group cooperates closely with other MRM chairs and also with non-university research institutions.
Another research focus is the generation of interpenetrating materials, e.g. by means of gas pressure infiltration and metallic die casting. A gas pressure infiltration plant has been set up and put into operation at our department for this purpose (see picture on the right). At up to 800 °C and 80 bar pressure, previously evacuated hollow structures, such as highly porous ceramic foams, can be infiltrated. As a result, the classic division into matrix and reinforcement no longer applies to this material class of interpenetrating composites, since the materials involved penetrate each other completely.
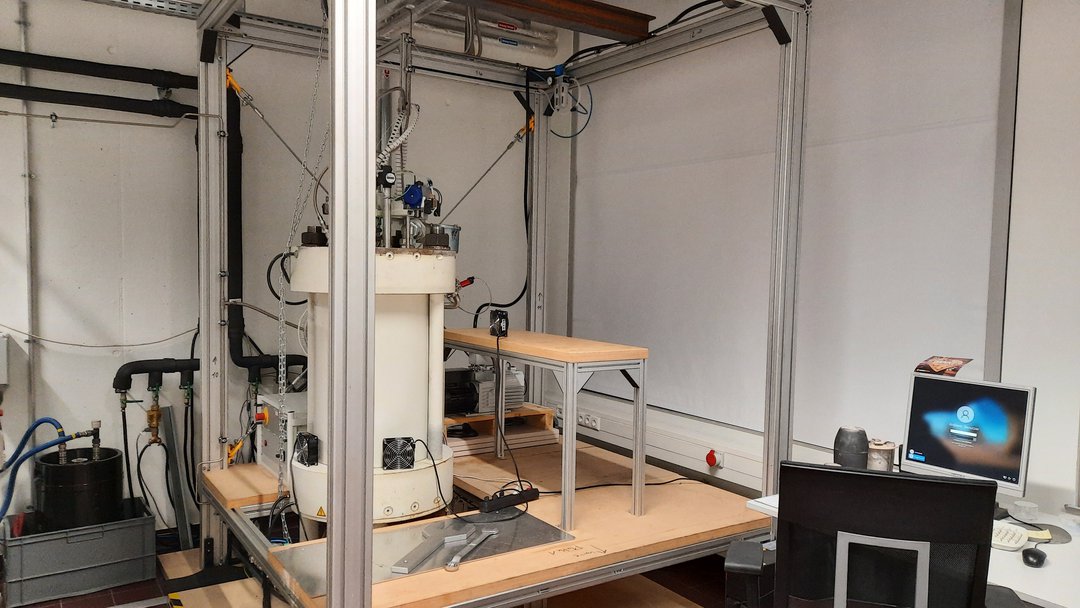
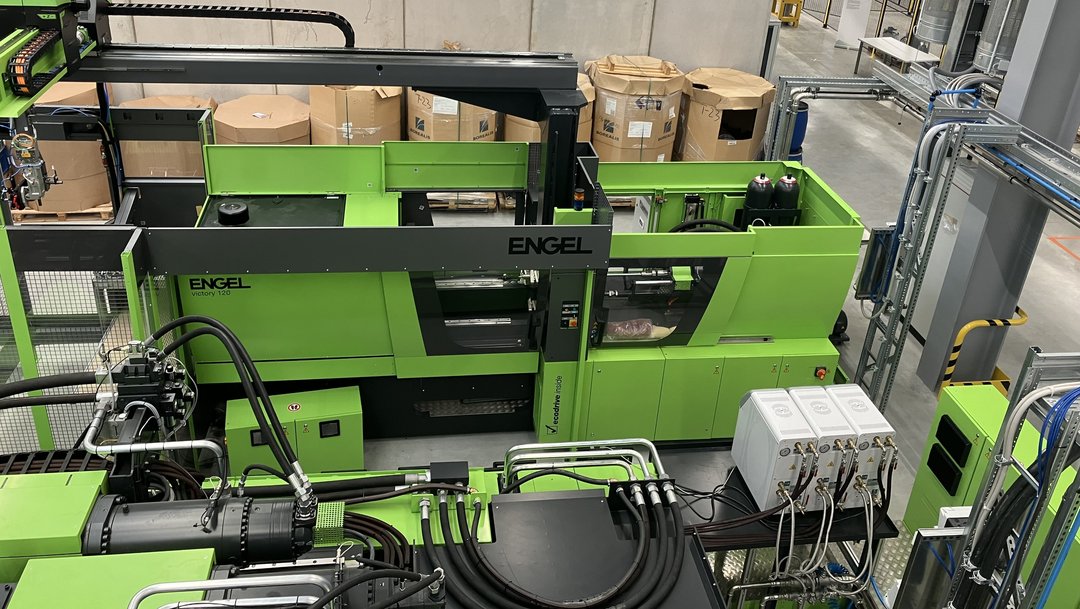
At the moment, the focus is still on metal-based systems, but here, the plastics processing methods mentioned offer great potential, too.
Thanks to metal die casting in the ENGEL Victory XY, inductively fusible alloys up to approx. 1000 °C can also be processed under vacuum and high cooling rates, so that amorphous metals can also be produced and introduced as an interpenetrating phase in high-melting, open-pore systems.
Additive manufacturing rounds off the working group's range of process diversity and forms an important interface to ceramic and metallic interpenetration composites, as well as open-pored systems produced with great freedom of form for subsequent infiltration, and the possibility of combining construction and functional materials and using them in hybrid materials alongside the structural component. But also the expansion of the product range of polymer-based materials, the introduction of functionalized layers, but also the feasibility of self-healing mechanisms complements the field of hybrid materials through fused deposition modeling 3D printing.
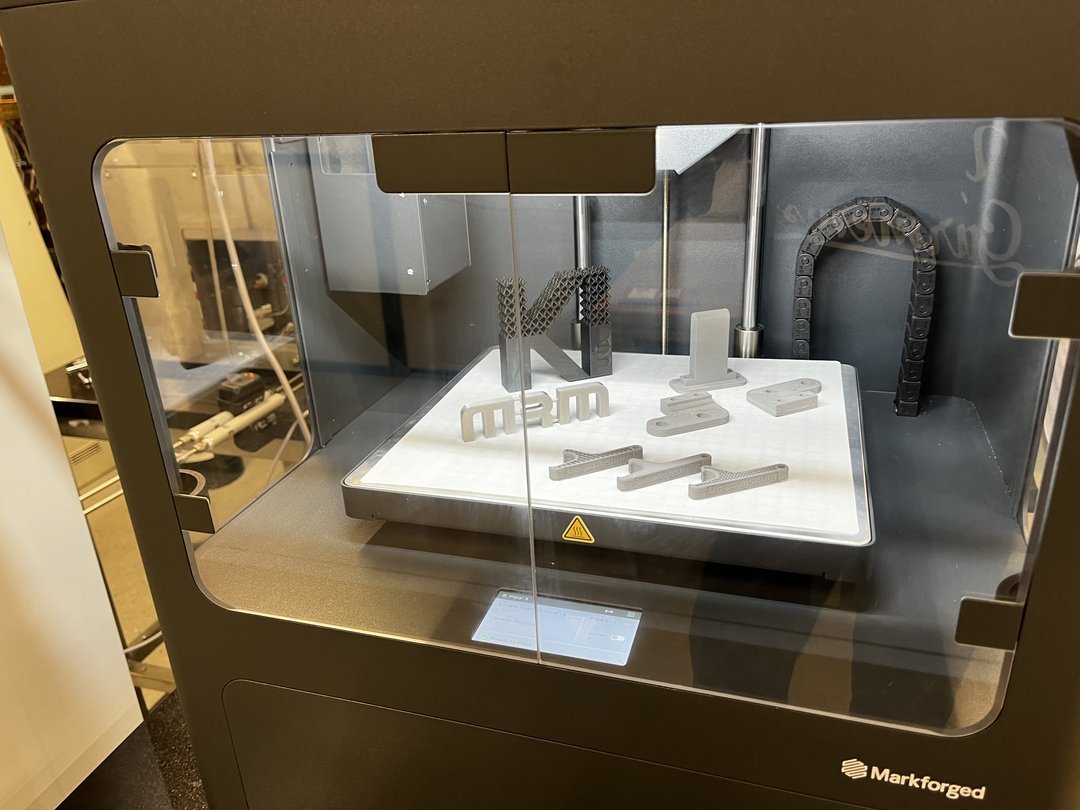
Team
Scientific Assistants
- Phone: +49 821 598 - 69156
- Email: marc.lindorf@uni-auni-a.de ()
- Room 203 (Building WALTER Technology Campus Augsburg / Gebäude 45)
- Phone: +49 821 598 - 69189
- Email: philipp.morbitzer@uni-auni-a.de ()
- Room 207 (Building WALTER Technology Campus Augsburg / Halle 43 Future Fabrication)
- Phone: +49 821 598 - 69179
- Email: frederik.siegmund@mrm.uni-augsburgmrm.uni-augsburg.de ()
- Room 207 (Building WALTER Technology Campus Augsburg / Halle 43 Future Fabrication)
- Phone: +49 821 598 - 69398
- Email: michael.volk@uni-auni-a.de ()
- Room 205 (Building WALTER Technology Campus Augsburg / Halle 43 Future Fabrication)
Current research projects
Information on our current research projects can be found here.