Research Infrastructure
Additive manufacturing
In the subfield of additive manufacturing, our focus is fused filament fabrication. Here, a component is created layer by layer form a polymer filament by melting it. In addition to common materials, fiber-reinforced polymers can be processed. Besides shortfiber reinforcement, it is also possible to incorporate continuous fibers. It is possible to map the complete material cycle. From filament to component and back again. Shredders and machines to produce filaments are available for this purpose. Furthermore, a system to produce metallic components is available. Apart from fused filament fabrication, a wide variety of duromer components can be produced using stereolithography.
The research focus is on thermoplastic and duromer-based composites as well as hybrid composite materials (polymer-polymer, metal-polymer, metal-metal) and the use of sustainable material systems or the use and development of recyclable material and component concepts. Some composites are created entirely in 3D printing, while others are scaffold structures which are then hybridized in further processes.
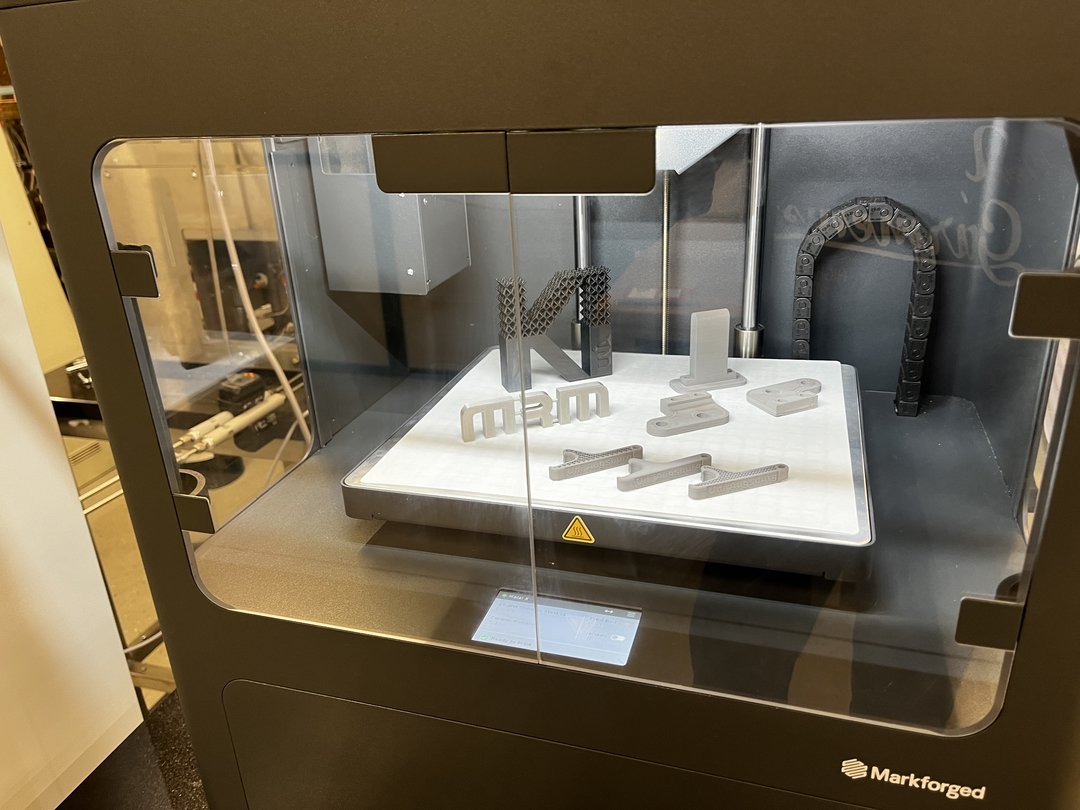
Additive manufacturing of structurally optimized lightweight structures made of fiber-reinforced building materials (FIBRACreator)
With a yearly production of more than 4 billion tons worldwide, cement is the most widely used material. However, its production contributes to around 8 % of annual global CO2 emissions.
Additive manufacturing, specifically the 3D printing of cements, makes it possible to save resources as functionally optimized structures can be created. The addition of short carbon fibers to cement leads to considerable increases in strength and thus enables rebar-free structures. With the FIBRACreator production cell in the AI production network, we are developing the additive manufacturing of lightweight objects made of FIBRACrete, a carbon fiber-reinforced cement developed at the University of Augsburg. The fiber reinforcement of the material leads to additional challenges in design planning and the 3D printing process, for which 6-axis robot is used in the FIBRACreator. Artificial intelligence (AI) methods are used for structural optimization, considering the alignment of short fibers along the tensile trajectories and thus reduce material and costs.
Applications are in the field of multifunctional building facades, parametric architecture, as well as in the restoration of listed buildings.
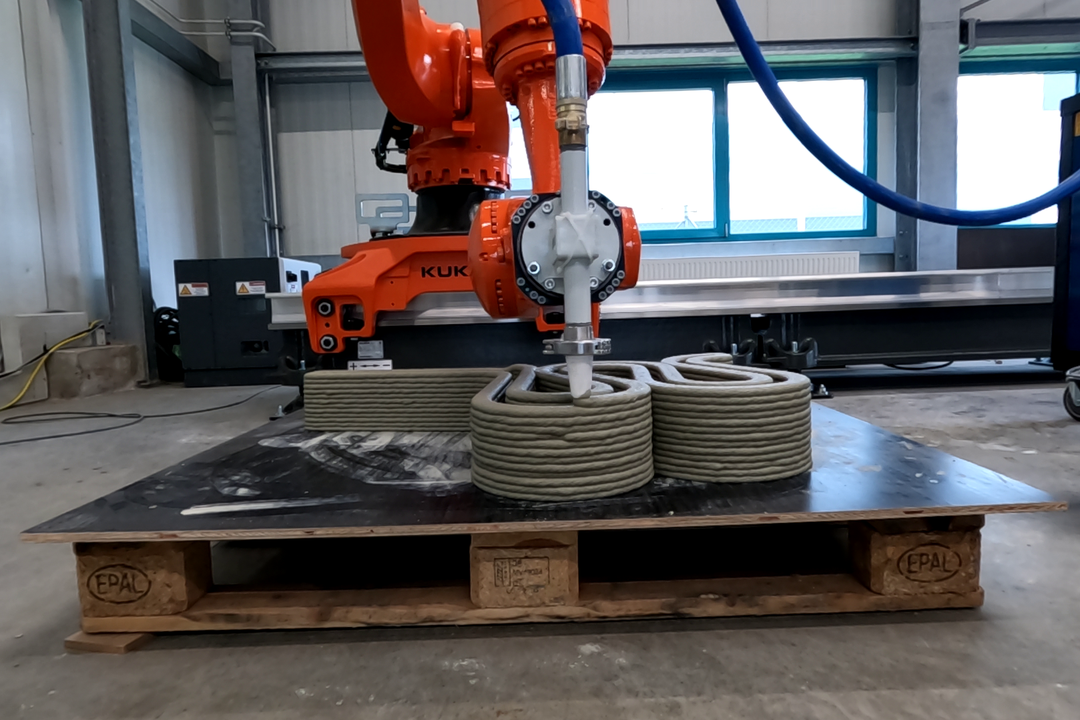
CNC
The Computerized Numerical Control cell covers a broad spectrum of machining processes with three different systems. A high-speed 5-axis system and a 3-axis milling machine are available for machining plastics, steel and non-ferrous metals. Of particular interest is, among other things, the possibility of high-speed machining of fiber composite materials at up to 75,000 rpm. In addition to these systems, a five-axis universal turning center is also available for the production of non-rotationally symmetrical turned parts. The systems help in the field of sample preparation as well as component manufacturing for the Halle 43 – Future Fabrication. They are combined with other manufacturing processes, such as additive manufacturing, to obtain optimal surfaces. The researchers monitor the processes with different using cutting edge sensor technologies and evaluate the resulting data using artificial intelligence methods. In addition to concepts for process documentation and real-time monitoring, the University of Augsburg is also researching methods for predictive maintenance or optimized tool exchange.
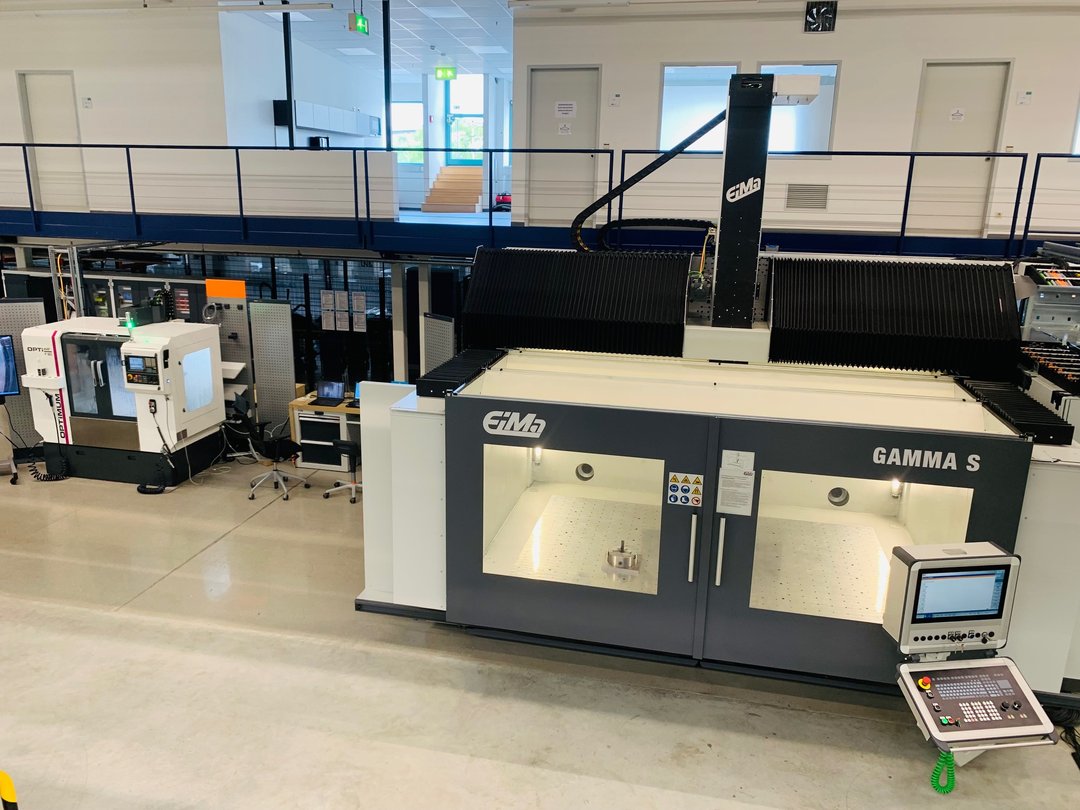
Computed Tomography Systems
Computed tomography (CT) systems use X-rays for non-destructive testing of components. Such systems are used, among other things, for precise component testing in development and during series production. CT X-ray technology provides a non-destructive insight into components. For conventional computed tomography systems, the size of the objects to be examined is often severely limited with tolerable dimensions of up to one meter. Llarger components or systems can only be scanned with highly specialized equipment. The solution to this problem is a cutting-edge robotic tomography system. Two collaborating robots form the heart of the system, one carrying the X-ray source and the other the detector. This enables scanning of large and complex geometries. The flexibility of the robots also allows a wide variety of inspection tasks to be handled with just one setup. The system therefore enables the examination of components created in the Halle 43 – Future Fabrication, and feedback of this information into production for process optimization. In addition, smaller plants or testing machines can also be monitored in-situ using the CT the system.
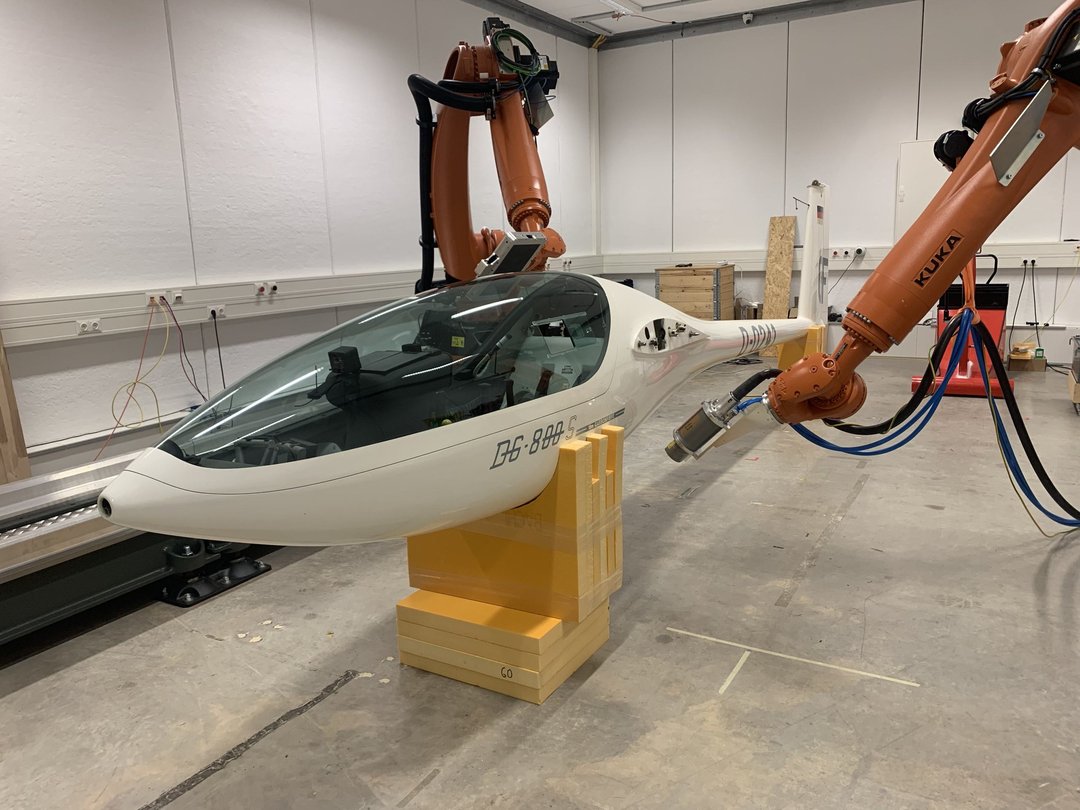
Friction Stir Welding
Compared to other joining processes, Friction Stir Welding (FSW) is a new type of joining process and is used in various industries such as aerospace, the automotive industry or railways. The FSW process is particularly suitable for metals and alloys that are difficult to weld. Different types of equipment can be used for this, such as a robot-based system or a gantry system. Robot-based FSW offers the advantage of more flexible geometric path guidance, whereas the strength of gantry systems lies in the joining of simpler geometries with greater process forces and high shape and position tolerances, especially in series production.
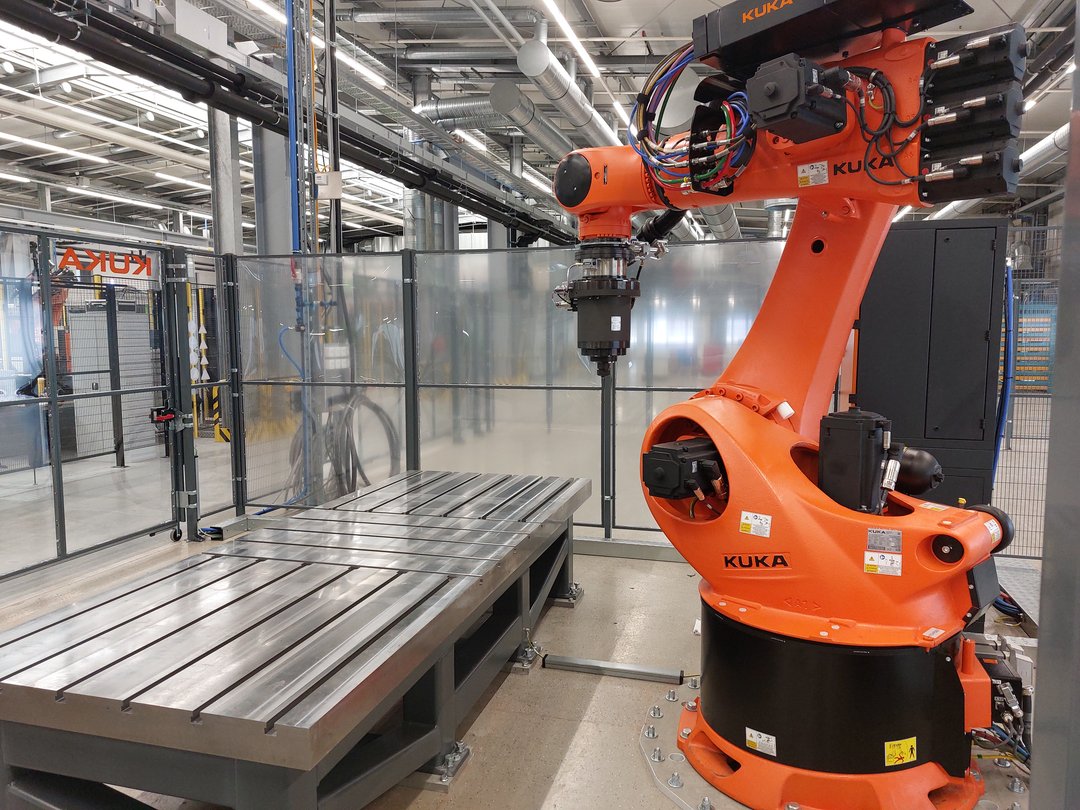
Hybrid Injection Moulding Facility
For the hybrid injection moulding process, a complex system consisting of a vertical clamping unit, mobile mould slide and 2K plastification units in combination with the injection moulding of metallic components (especially metallic glasses) is available. The vertical clamping unit, together with the mobile mould slide, enables the easy insertion of semi-finished products such as fibre-reinforced tapes or recycled fabrics. With the plasticising units, thermoset, thermoplastic or physically foamed polymers can be processed in any combination in 2K injection moulding, resulting in optimum process and material variability. The combination of (fibre-reinforced) polymers with the injection moulding of metallic components and the automated process linkage opens up further exciting possibilities for developing and producing hybrid materials in a near-series environment.
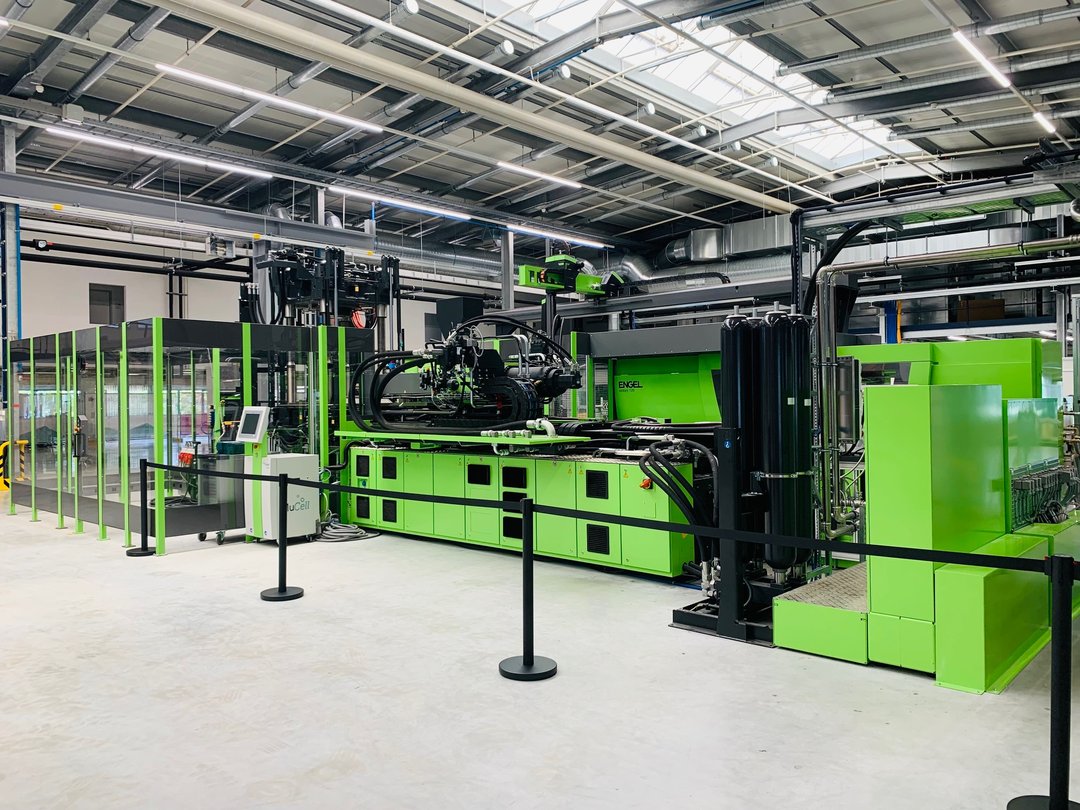
Laser Cutting System
With a laser cutting system, ventilation technology and small, robot-supported logistics, the research cell replicates a typical industrial production process. The aim is to answer application-oriented questions in the areas of manufacturer-independent networking, batch size 1 and process organization and to research new solutions together with industrial partners. They form the basis for testing new business and production models, such as the formation of a digital value creation network for the implementation of cloud manufacturing. The networking solutions combined with semantic-interoperable data and process models also provide the basis for developing AI models, e.g. for process organization, and testing them in an industry-related environment.
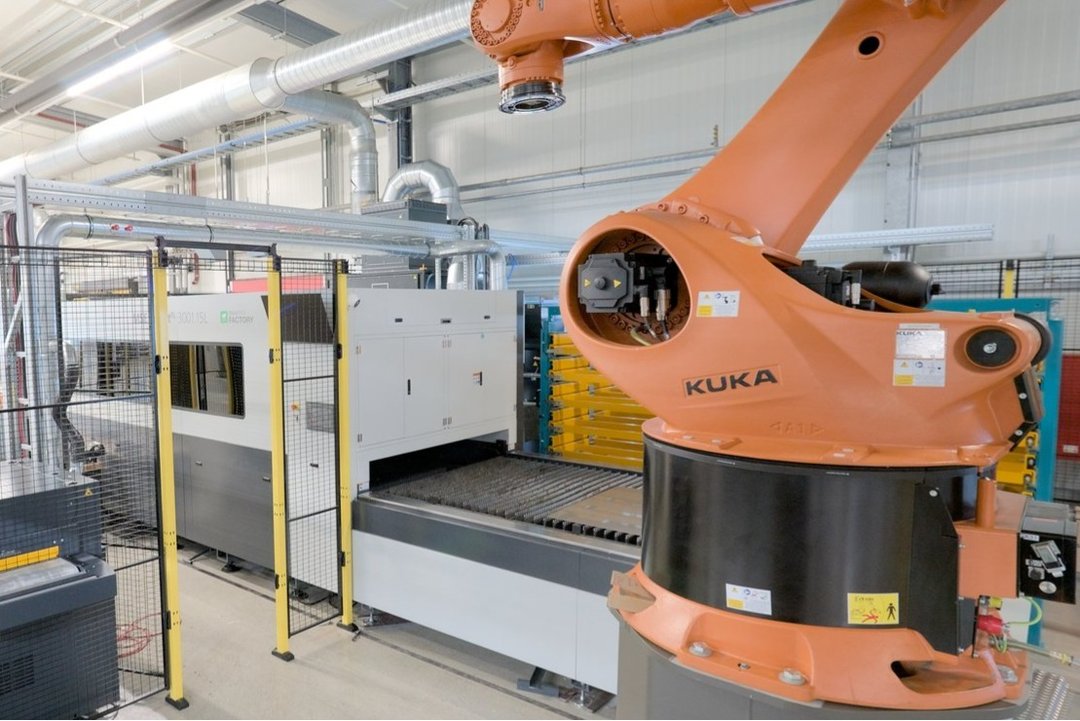
Mixed Robotics
In the "Mixed Robotics" cell, the focus is on developing a flexible machining and handling robot cell. The goal is to enable various types of robots, such as industrial robots, collaborative robots, and mobile robots, to collaborate with each other and with humans. The research focuses on the development of plug-and-produce concepts, multi-robot-collaboration, and human-robot-collaboration. Additionally, the study explores how AI-based methods can be used to detect humans in the vicinity of robots, as well as how machining and handling processes can be planned and optimized.
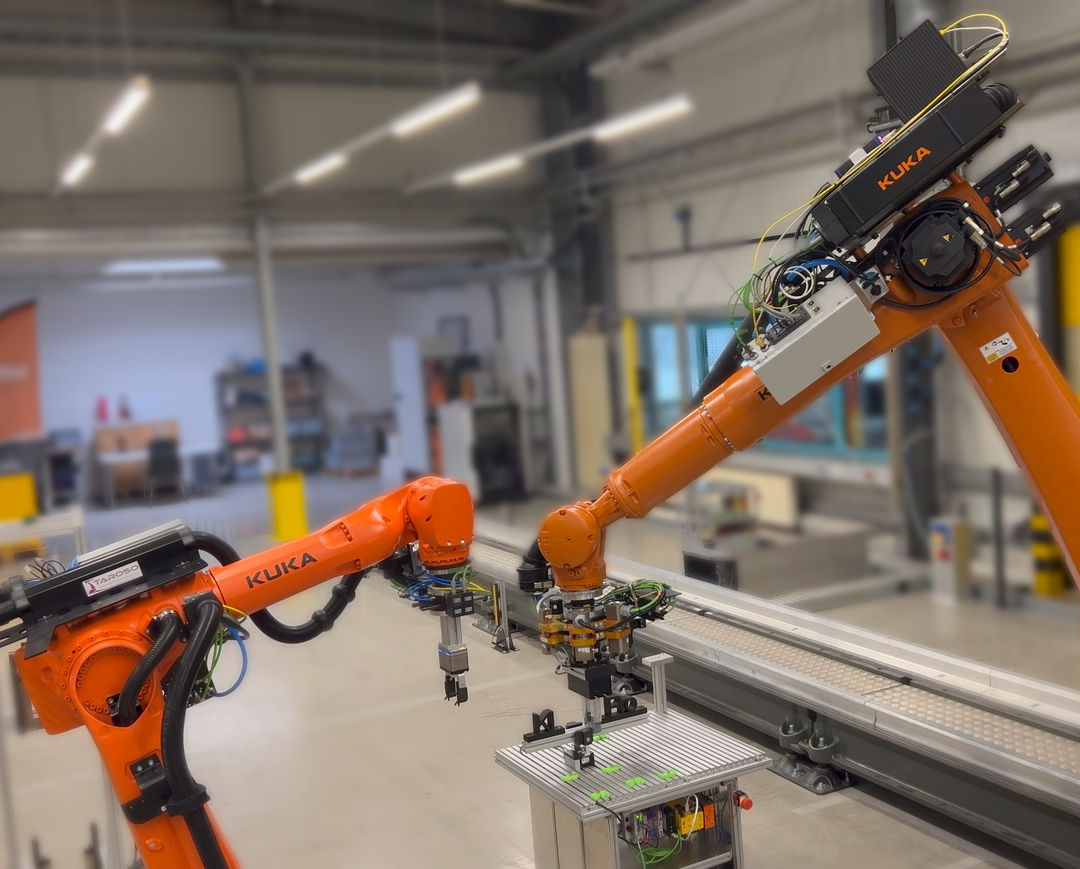
Robot-Based Component Testing
The research objective of robot-based component testing is the implementation of a flexible test bench for the mechanical characterization of components, which are, for example, produced in Hall 43. The testing cell consists of two heavy-duty robots for applying loads to the test specimen, each equipped with force-torque sensors, a clamping field for mounting the test specimen, and a linear test cylinder for additional loads. In addition, an optical sensor is available to measure the deformation of the component. The major advantage of this system compared to conventional test benches or testing machines lies in its flexibility, the diverse possibilities for applying loads, and the potential size of the components to be tested. The current scientific challenges involve planning complex test motions, programming dynamic robot applications, and automating specific tests.
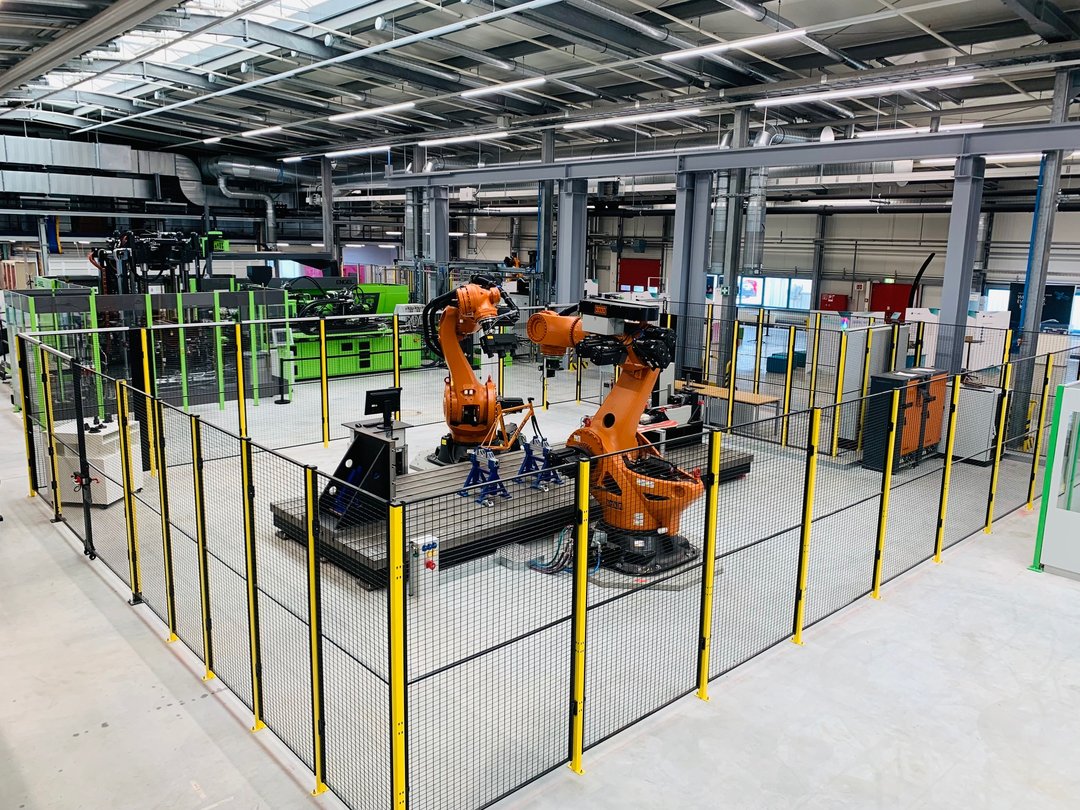
Cooperations Desired!
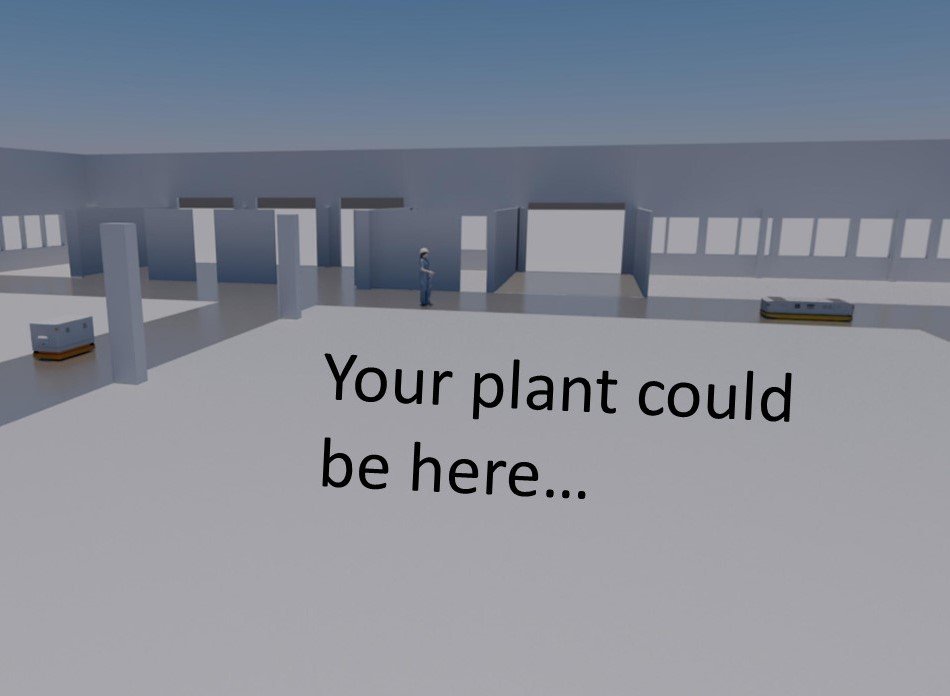
Our modular system allows you to integrate your own system with us. For such a cooperation, we offer individual approaches and characteristics. Please feel free to contact us: